Carbon Fiber & Composite Materials
324 products.
Filter by Application
[Close]
24 products.
[Close all]
Roller (CARBOLEADER ™)
[Close]
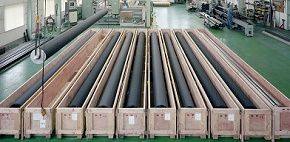
CARBOLEADER™ is a carbon roller that simultaneously offers light weight, high rigidity, and a high critical number of revolutions. It is used for a wide range of applications, including separators for rechargeable batteries, for optical applications and all kinds of films, for printing, and paper manufacture. It can significantly increase productivity and reduce costs by improving production quality and speed, and reducing defect rates.
C/C composite, C/SiC composite
[Close]
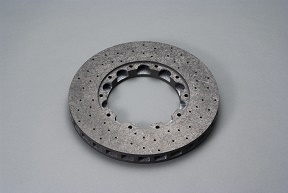
C/C (carbon fiber reinforced carbon) composites are made of carbon matrix reinforced with carbon fiber, and have high strength, high elasticity, high toughness, and ultra-high heat resistance, and can be used at temperatures above 1,000ºC.
C/SiC, also known as ceramic matrix composite (CMC), is a composite material with a ceramic matrix, and our CMC is reinforced with carbon fiber. It has higher strength and elasticity than C/C composite, and can be used in a wider variety of applications.
Golf Shaft
[Close]
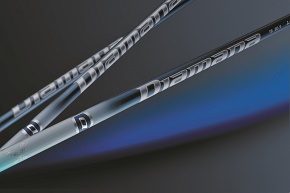
Golf Shafts Product Page - Carbon fiber has been developed into a leading material in the field of sports equipment, due to its excellent design flexibility and its superior heat and impact resistance. The share of CF shafts in the golf shaft market has been growing for many years, driven especially by strong demand for lightweights, and it continues to grow.
(CF shafts are produced by wrapping sheets of carbon fiber impregnated with epoxy resin, known as “prepregs,” around a metal core, and then curing at high temperature.)
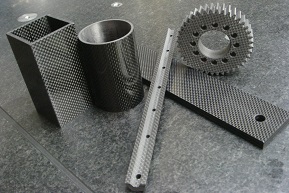
Carbon fiber composite materials, also known as carbon fiber reinforced plastics (CFRP), are composite materials made of carbon fibers and resin (mainly epoxy resin).
As light, strong, and hard materials, they are used in wide range of applications such as sporting goods, industrial, aircraft and automobile components. By selecting suitable resin, it is possible to add features like heat resistance, impact resistance, and flame retardant, and thus provide superior characteristics not found in conventional metals and ceramics to enable a reduction in the weight of parts, give freer design.
Carbon Fiber Paper (GDL)
[Close]
Carbon Fiber Pellets
[Close]
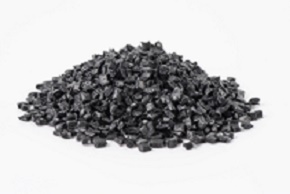
Carbon fiber pellets are thermoplastic molding materials created by blending carbon fiber with various resins to achieve performance that is superior to conventional reinforced resins. Advanced physical properties can be achieved by combining different base resins and carbon fibers, according to the specific application.
Carbon Fiber FMC (CF-SMC)
[Close]
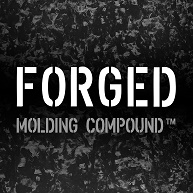
Carbon Fiber FMC (CF-SMC) is a sheet-type intermediate material made of cut high-strength carbon fiber impregnated with thermosetting resin. This material can be press molded, substantially reducing molding time compared to conventional autoclave or oven molding.
In addition, compared with carbon fiber intermediates of Continuous fibers, the random arrangement of Short fibers ensures fluidity and makes it possible to mold intricately shaped parts like those with ribs and bosses.
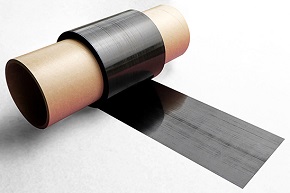
Under Development
Kyron™ ULTRA is a new sheet-like intermediate material developed by Mitsubishi Chemical, in which carbon fibers are impregnated with engineering plastics. It is a high performing carbon fiber composite material in the form of a UD (Uni-Directional) prepreg with carbon fiber in one direction.
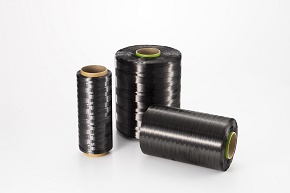
Carbon fiber is a high-strength and high-elastic modulus material, yet its specific gravity is only one-fourth that of iron. It, therefore, enables high strength, high rigidity, and weight-saving in a wide variety of applications.
Carbon fiber tow, made of bundles of untwisted filaments, is the essential material in our carbon fiber product line.
Carbon Fiber Fabrics
[Close]
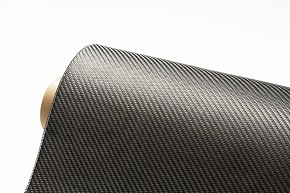
Carbon fiber fabrics have excellent drape properties which make them ideal for 3D shape applications. Due to the outstanding design possibilities they offer, carbon fabrics are also in high demand for applications that require visual appeal. As well as their design potential, carbon fabric materials offer excellent layup efficiency. You can layup a single ply in two directions.
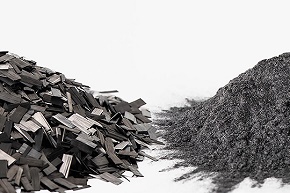
Carbon Chopped Fiber is a product made by chopping carbon fiber tow.
Carbon Milled Fiber is a product made by grinding milling chopped fiber into a powder (milled) form.
Chopped fiber is typically around 3 to 6 mm long, while milled fiber is typically less than 200 µm long. Both of these materials are used to enhance the physical properties of thermoplastic resins and rubbers, and to increase electrical and thermal conductivity.
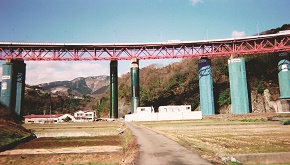
Compared with conventional steel plate or concrete-jacketed reinforcements, REPLARK simplifies construction and shortens construction period by eliminating the need for heavy machinery. For its high strength, lightweight, high durability, and excellent workability, REPLARK has earned an outstanding reputation for the repair and reinforcement of bridge piers, floorboards, columns, chimneys, and for other structural applications.
e-Plate/Leadline: This repair and reinforcement material enables reinforcement by simply attaching or embedding prefabricated carbon fiber reinforced plastics (CFRP), without the need for resin impregnation or for layering the required amount of reinforcement, as in the case of repair and reinforcement using carbon fiber sheets, thereby reducing construction time and improving construction quality.
- Product Finder
-