Case Study
Space
Carbon fiber reinforced plastics (CFRP) are in more general use in the space sector, where the need for weight reduction is greater than in the aircraft sector.
They are used in rockets and space shuttles, but here we introduce a case study of application to artificial satellites.
Artificial Satellites:
Excellent dimensional stability in harsh environments
Carbon fiber reinforced plastics (CFRP) are indispensable materials for space development. Their excellent specific strength and elasticity modulus, as well as high dimensional stability, maintained even in environments with extremely large temperature changes, have enabled high-precision observations in space.
Achievement of
components with zero coefficient of thermal expansion (CTE)
Carbon fiber has high dimensional stability due to its low thermal expansion coefficient, approximately 10% that of metal.
Furthermore, use of pitch-based, high-elasticity-modulus carbon fiber, which has a negative coefficient of thermal expansion, makes it possible to design components with a zero coefficient of thermal expansion.
High elasticity modulus and strength enable the design of lightweight components whose weight is reduced as much as possible, which reduces launch costs and energy requirements.
As shown by numerous launch records, CFRP shows stable performance even in the harsh radiation environment of space.
K13C2U, a pitch-based, high-elasticity-modulus carbon fiber, has the unique property of a negative coefficient of thermal expansion, which is used to balance out the positive coefficient of thermal expansion of the resin, and thus achieve a zero coefficient of thermal expansion. This material is used in solar observation satellites as a support material for optical instruments, contributing to high-precision observations.
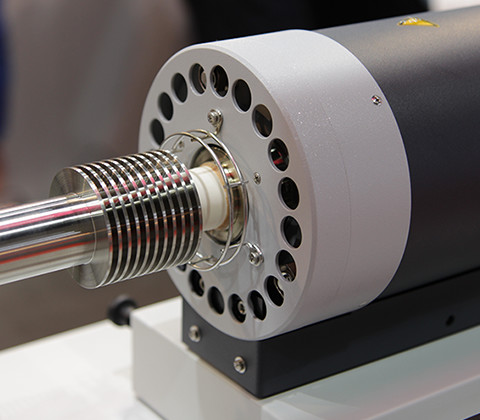